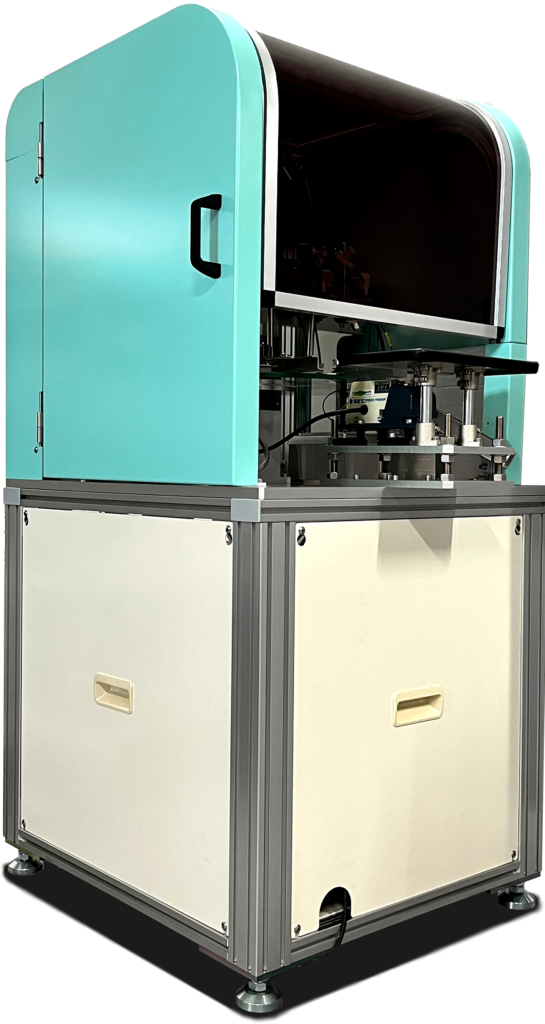
Inspects small plastic and metal parts up to ◆30mm square Inspection of two sides of front and back The inspection is performed on the front and back sides of small plastic and metal parts up to 30 mm square.
◆On a glass disk To image and inspect the front and back without inverting without inverting the glass disk. High-speed processing The process can be performed at high speed.
Is it the same image as the good one? Is the image the same as a good one? This is a simple and reliable inspection method.
◆Installed users achieved Achieved 4x speed Additional orders have been placed. We have received additional orders.
\Samples can be evaluated free of charge/.
GlamichanFeatures of
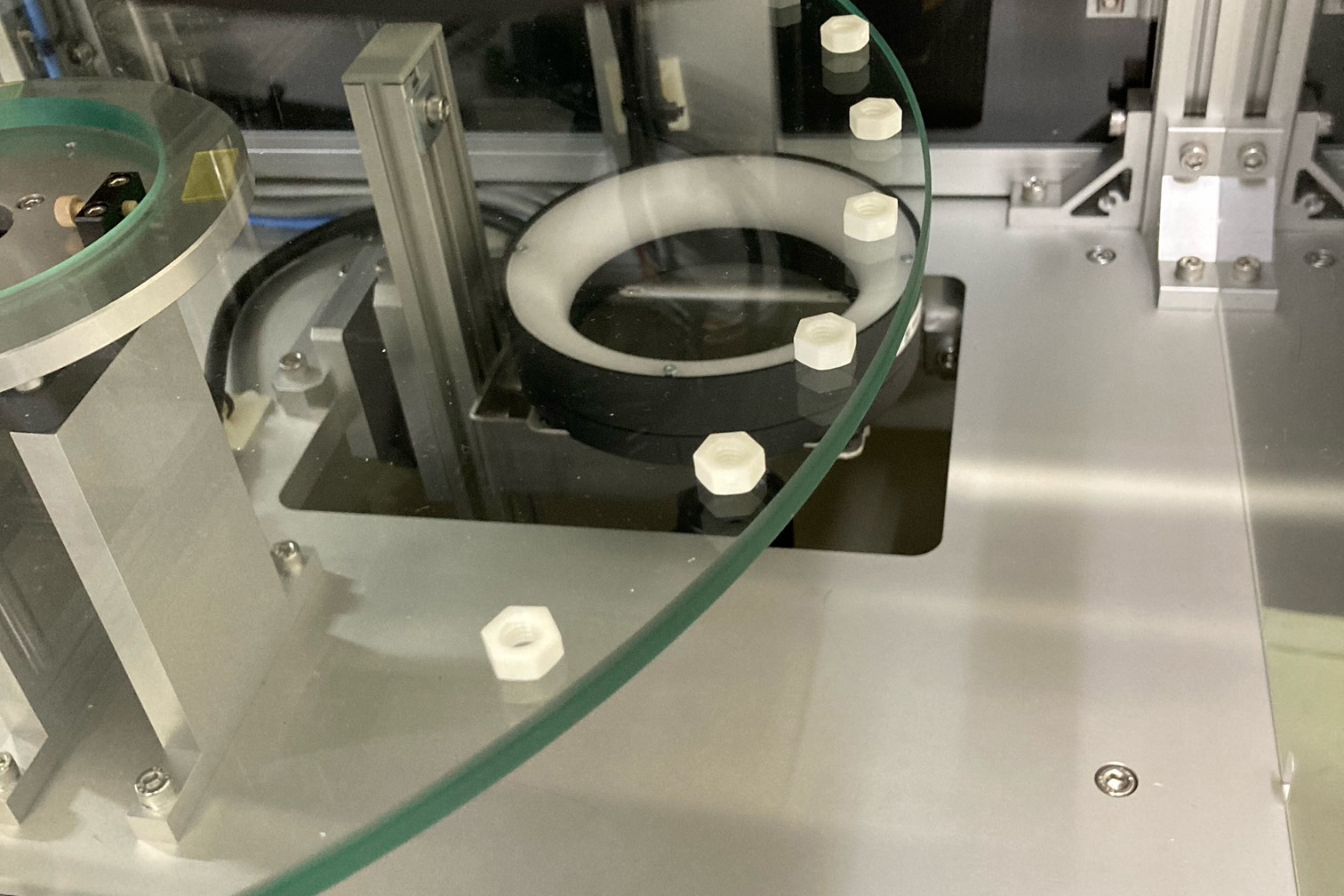
High-speed inspection of the front and back 2 sides of small parts up to 30 mm square
The front and back cameras capture images on a rotating glass disk for inspection.
High-speed processing is possible because there is no mechanism such as a front-to-back reversal.
The size is limited to 30 mm square in order to provide detection capability at the level of visual inspection.
Simple mechanism allows visual inspectors to work 4 times faster or more
The strongest cost performance in our 22 years of experience.
Capable of inspecting 2 to 10 pieces per second. Achieved "4 times faster" in user evaluation.
Simple and versatile mechanism. Easy maintenance.
"Is it the same as a good one?" The easiest and most reliable
It is both easy to use in the field every day and reliable to ensure zero leakage.
Good products are sorted by registering images of good products and inspecting whether the images are the same as the registered images.
If there is a large variation in the number of good products, the variation can be tolerated by registering a large number of good products.
Inspection method with more than 1000 units in operation
Almost all lines (more than 400 units) have been adopted by customers, and some customers are continuing to introduce the system and have reached the 100-unit scale.
In addition to comparing good products, the system also supports dimensional inspection, character reading, and other standard functions.
The first user of this system installed 5 units in a row.
Flexibility for "more."
- Deep learning functionality for more accurate determination of good variation and higher good quality rate
- LumiTrax machine (KEYENCE) that visualizes and detects defects that cannot be seen unless agitated by hand.
- Parts feeder function for unattended continuous operation
- Additional camera for multi-sided inspection
GlamichanInspection Examples
Published in Metoree
GlamichanOur YouTube video featuring an example of an inspection of a "M" was featured on Metoree (https://metoree.com/articles/523/ ), an information portal site for engineers!
Facts and Figures! Glamichan The first user
~ For precision plastic molding manufacturers
Although several imaging inspection systems had been installed, they were difficult to operate and there were concerns about the inspection results, so they were not fully operational.
AT FIRST, THE FIS-100 WAS USED IN THE "PING-PONG METHOD" (HAND-FEEDING AND HAND-REMOVING UNDER THE CAMERA). ALTHOUGH IT WAS WORKING WELL, A FASTER PROCESSING METHOD WAS REQUIRED.
Therefore, we proposed a method of inspecting the reverse side by placing it on a glass disk, and manufactured the first unit using the "manual feeding into the equipment and automatic sorting" method. As a result, the results exceeded our expectations.
In addition to the inspection speed, the compactness of the device and its quiet operation were also highly evaluated.
Around this time, the designer started calling it " Glamichan", which became its nickname.
Additional orders were immediately received. With a clear return on investment, the budget became easier to obtain, and it was decided to combine the high functionality of the system.
A Keyence LumiTrax camera has been introduced to enhance detection capability for shape defects.
A 6-sided inspection version with an additional side camera has also been introduced.
Currently, workers manually feed the parts at high speed during the daytime, and the parts feeder is operated unmanned during the nighttime. The workers compete with each other to see how many parts they can feed in, as if it were a game," he says.
This is an example of the "Happy Visual Inspection " we aim for.